Hidas Bálint 2025.02.03.
A visszamodellezési munka nagy része a QuickSurface nevezetű célszoftverben történt, míg a tervezési munka további része Autodesk Inventorban lett elvégezve. A program számos olyan eszközt biztosít a felhasználó számára, mellyel gyorsan és hatékonyan elvégezhető a hálómodellre épülő CAD modell felépítése. Az elkészült modell könnyedén exportálható a modelltörténettel együtt az Autodesk Inventor, illetve a SolidWorks programokba, ahol szükség esetén további módosítások eszközölhetők.
Modellezés bemutatása
A modelltérbe történő importálás után az első lépés a háló origóba illesztése volt, ezzel biztosítva a későbbiekben a könnyebb modellezést. Ehhez az illesztéshez geometriai referenciák lettek felvéve a hálómodellen. Elsőként az járókerék alapját képző középső tárcsa egyik homlokfelületére lett sík illesztve a megfelelő hálórégiók kijelölését követően.
A sík és a homlokfelület illeszkedésének minősége kiemelt fontosságú. A későbbiekben ebből az alapsíkból lett származtatva további kettő darab geometriai referencia, így az esetlegesen fennálló pontatlanság azok esetén is megjelent volna. Az illeszkedés pontossága ellenőrizhető a szoftverbe beépülő eszköz segítségével.
1. Kép: Hálószegmensre illesztett sík
Ezt követte a forgástengely definiálása, mely esetén a járókerék forgástengelyét egyértelműen meghatározó tengely külső palástjára lett hengeres elem illesztve. Ennek a hengeres elemnek a középtengelye megegyezik a járókerék forgástengelyével. Az előírt kényszerek értelmében a létrehozott tengely az alapsík normálisa. Ahhoz, hogy a modell minden szabadságfoka le legyen kötve, egy a már létrehozott referenciákból származtatott sík létrehozására volt szükséges, mely merőleges az alapsíkra és egybeeső a középtengellyel.
A létrehozott geometriai referenciák segítségével a háló könnyedén eltolható volt a modelltér origójába. Kényszerként lett előírva a forgástengely és a z tengely egytengelyűsége, az xy sík, valamint az alapsík egybeesése. Végezetül szintén egybeesőként lett definiálva az yz sík és a származtatott sík. Ezzel a három kényszerrel a hálómodell összes szabadságfoka lekötésre került, pozíciója egyértelműen meg lett határozva a térben.
Az origóba illesztett hálómodell, valamint a felvett geometriai referenciák a 2. ábrán figyelhetők meg.
Az alkatrész kialakítását, valamint a funkcióját figyelembevéve feltételezhető, hogy az alkatrész forgásszimmetrikus, továbbá, hogy van szimmetriasíkja. Ezen két állítás értelmében a lapátok geometriája és kiosztása, mindkettő lapátsor esetén, megegyezőnek feltételezhető. Ebből adódóan a visszamodellezéshez elegendő volt a háló egy bizonyos szegmensének felhasználása. A további hálóelemek el lettek tüntetve, csak az ellenőrzési fázisokban lettek megjelenítve. Ennek a lépésnek előnye, a megjelenítéshez szükséges kisebb grafikus hardver igény, valamint az átláthatóbb modelltér. Elsőként az alaptárcsa lett létrehozva. A körbeforgatott profil a kiemelt hálószegmens elmetszésével létrehozott ponthalmaz alapján lett megrajzolva. A méretek egy része a fizikai alkatrészről lett lemérve, míg a többi a hálómodellen alapszik. A megrajzolt profil a z tengely körül lett körbeforgatva, ezzel létrehozva az alaptárcsát.
2. Kép: Az alaptárcsa létrehozásának lépései
A lapátok elkészítése során az utolsó lépés az ellenőrzés volt, mely magába foglalta a felület folytonosságának vizsgálatát, valamint az illeszkedés minőségét egyaránt. A zebracsíkos megjelenítés alkalmazásával megállapítható volt, hogy a lapátok külső és belső felületén felület folytonossági hiba nem jelentkezik. Az eltérésvizsgálat eredményei alapján pedig a kialakított geometria elfogadható.
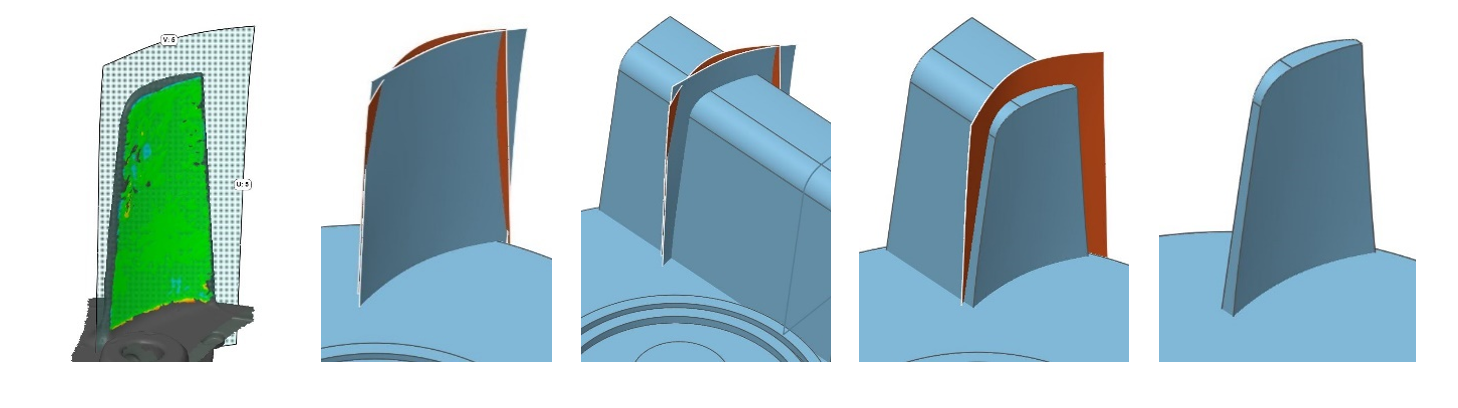
3. Kép: Lapát létrehozásának folyamata
Ezt követően a lapát körkörösen kiosztásra került az alaptárcsára, majd az így létrehozott lapátsor tükrözésre a tárcsa másik oldalára. Az alkatrészen további részletek lettek kidolgozva, melyek megtalálhatók az eredeti alkatrészen is. Mivel a tengely a későbbiekben került megtervezésre, így annak furata a járókeréken a CAD szoftverben lett kialakítva. A visszamodellezés utolsó lépése az elkészült modell és a háló közötti eltérési értékek vizsgálata volt. Az eltérési értékek mértéke elfogadhatónak tekinthetők. Ezek elsősorban az eredeti alkatrész gyártástechnológiájából adódó pontatlanságokra vezethetők vissza és az üzem során esetlegesen beálló maradandó alakváltozásokra. Az elkészült CAD modell modelltörténettel együtt exportálásra került Autodesk Inventor-ba, ahol további munkálatok lettek elvégezve, ami magába foglalja a tengely megtervezését, valamint a járókeréken lévő tengelyfurat kialakítását. Itt lett továbbá elkészítve a járókerék gyártási dokumentációja. A nyers CAD modell, valamint az eltérésvizsgálat eredménye a 6. ábrán látható.
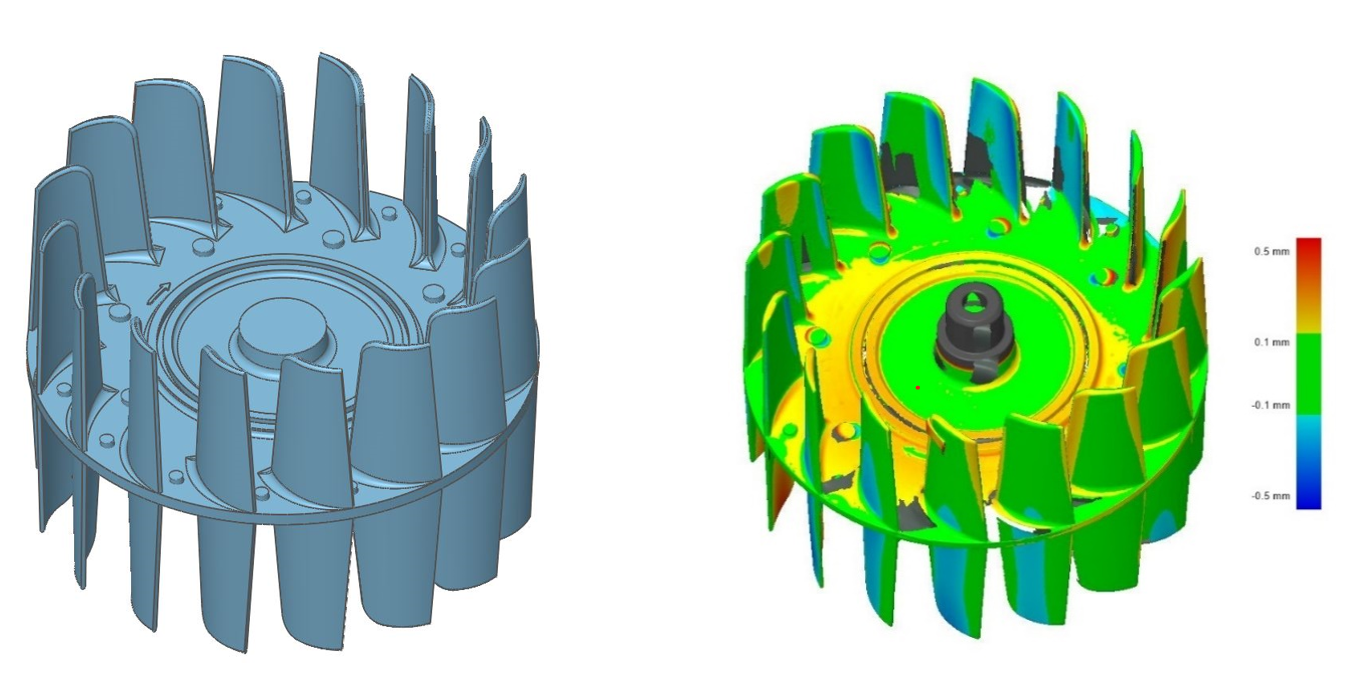
4. Kép: A kész CAD modell, valamint annak illeszkedése a hálómodellre
Modell modósítása
Az alkatrészen a CAD szoftverben elhelyezésre került a központi furat, mellyel párhuzamosan meg lett tervezve a tengely. Az eredeti járókeréken két oldalról egy-egy persely volt elhelyezve az alkatrészen, az egytengelyűségi problémák elkerülése érdekében ez a két persely egy darab tengellyel lett kiváltva. A tengely esetében fontos követelmény a levegő nedvességtartalmával szembeni korrózióállóság. E szempont figyelembevételével, valamint az anyag kedvező árát is szem előtt tartva, a CuZn39Pb3, azaz a 18 mm átmérőjű sárgaréz kör rúd került kiválasztásra. A tengely és a járókerék furatába ragasztással került rögzítésre. A furatban, valamint a tengelyen barázdák lettek elhelyezve, melyekkel növelhető a ragasztott kötés szilárdsága.
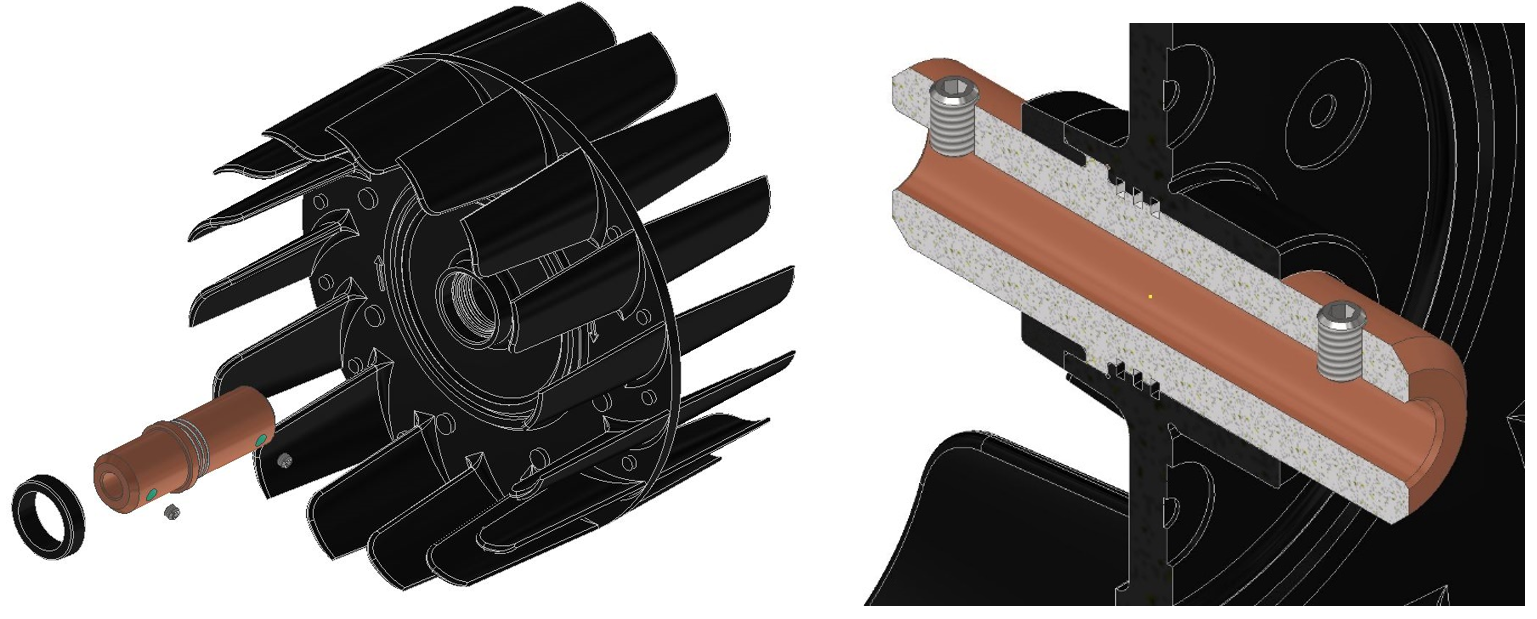
1. Kép: A járókerék összeállítása
A járókerék robbantott ábrája, valamint a tengely elhelyezkedése a 7. ábrán látható. Már a tervezés során egyértelmű volt, hogy ez a technológia a modell orientációjától függetlenül alkalmatlan erre az alkalmazásra megfelelő furatot nyomtatni. A modellben a furat anyagráhagyással lett elkészítve, így a nyomtatást követően a furat méretre lett esztergálva. Ezt követően a modellen el lett végezve egy végeselem szimuláció, mely alapján a modell módosítására nem volt szükség.