Hidas Bálint 2025.02.03.
A tervezési folyamatot követte a gyártás, mely magába foglalta az alkatrészek nyomtatását, a járókerekek készre szerelését, a felület kezelési lehetősége vizsgálatát, valamint a kerekek kiegyensúlyozását egyaránt.
Alkatrész nyomtatása
A CAD szoftverből STL formátumban exportált fájl a Formlabs saját szoftverébe a PreFormba lett importálva. Figyelembe véve, hogy az alkatrészből egy autóba kettő darabra van szükség, ezért ennyi került kinyomtatásra. Az alkatrész kialakításából adódóan azok, könnyedén összeforgathatók. Ezzel csökkenthető a nyomtatási helyszükséglet, mely magával hozza az össze nem olvasztott por mennyiségének csökkenését, melyet minden esetben célszerű minimalizálni. Az alkatrészek a nyomtató kamra közepére lettek pozícionálva, úgy, hogy a forgástengely a z tengellyel párhuzamos. Ezzel a két lépéssel biztosítható volt a nyomtatás utáni egyenletes hűlés, valamint az alkatrész forgásszimmetriájának megtartása.
Az alkatrészek elhelyezését követően a programon belül lehetőség van a nyomtató, valamint a nyomtatott anyag kiválasztására. Ebben az esetben a gép Fuse 1+30W, míg az anyag PA11CF-nek lett választva. Ezek után a gyári szoftver automatikusan beállította a géphez és anyaghoz megfelelő paramétereket, azok módosítására nem volt lehetőség.
Ezt követően a szoftver meghatározta a nyomtatáshoz szükséges időt, amely 14 óra és 36 percre adódott. Ezt követte egy 12 óra 29 perces hűlési folyamat, melynek szerepe kiemelkedően fontos. Amennyiben az egyenletes hűlés nincs biztosítva a nyomat elvetemedhet. A programból megállapítható továbbá, hogy összesen 3,03 kg por került felhasználásra nyomtatás során, ennek 14%-a került összeolvasztásra, vagyis közel 0,43 kg. Látható továbbá, hogy 1550 réteg került kiterítésre a por 0,11 mm-es rétegvastagságban.
A géppel végzett minden nyomtatás előtt az előírt tisztítási műveleteket kell elvégezni. Az első ilyen lépés a nyomtatókamra hőmérsékletét monitorozó IR szenzor megtisztítása. A tisztítás 99%-os etanollal és szöszmentes mikroszálas kendővel történt. Ez a lépés kiemelten fontos, hiszen az IR szenzor felelős a nyomtatótér hőmérséklet szabályozásáért. Esetleges rendellenes működése hibás nyomathoz vezethet. További fontos lépés a nyomtatótér, és a kamra megtisztítása, valamint a portartály feltöltése kellő mennyiségű porral.
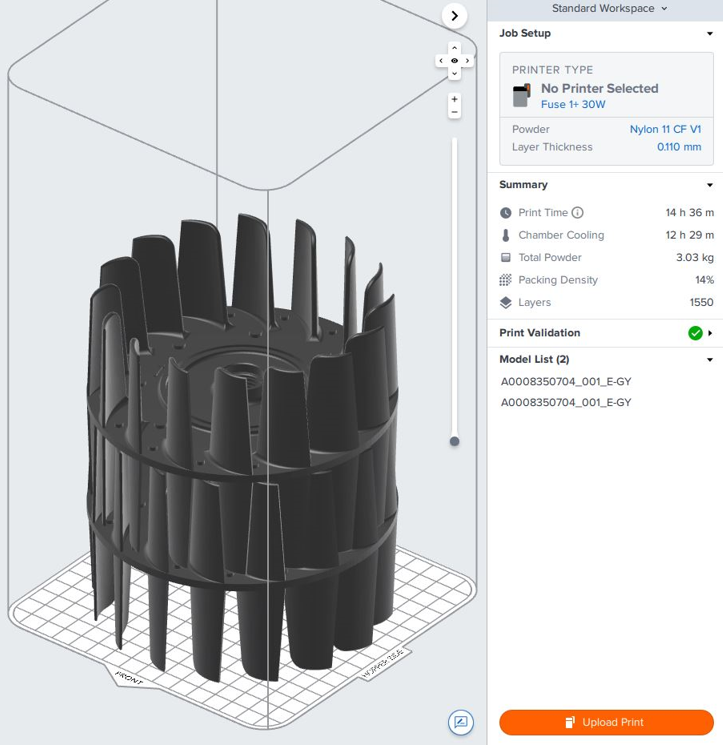
1. Kép: Alkatrészek elhelyezkedése a nyomtatótérben
A nyomtatást követően az alkatrészek a nyomtatóhoz tartozó utómegmunkáló állomáson lettek letakarítva. Ezt követően a felületen maradt kis mennyiségű por üveggyöngy szórásával lett eltávolítva.
Felületkezelés
A nyomtatott felületet porozitás jellemzi, mely hátrányos lehet olyan alkalmazásoknál, ahol a felület nedvesség lepergető hatása kifejezetten fontos. Továbbá bizonyos dőlésszögben álló felületek esetén a rétegvonalak tisztán kivehetőek, ezek esztétikai oldalról jelenthetnek problémát. Egy esetleges felületkezelés számos további előnnyel járhat, úgymint a környezetei hatásokkal szembeni ellenállóképesség növelése, valamint a mechanikai tulajdonságok javulása. Éppen ezért két lehetséges eljárás is kipróbálásra került.
Ezekre a problémákra nyújthat megoldás az úgynevezett vapor smoothing eljárás, mely során kontrollált körülmények között oldószert permeteznek a nyomtatott alkatrész felületére. Ez kismértékben megoldja a felszínt ezzel kiegyenlítve a felületen található egyenletlenségeket. Az eljárás előnye a felületi érdesség csökkentésén túl, hogy az így kialakult felület hidrofób, továbbá az alkatrész mechanikai tulajdonságai is javulnak. [39]
Megoldást kínál a Cerakote elnevezésű kerámia alapú festék, mely vékony rétegbe felhordva a felületre kemény és ellenálló réteget képez. A képződött felület kopás, karc, hő és UV álló, továbbá hidrofób tulajdonságokkal is rendelkezik. [40]
A felületet festés előtt megfelelően elő kell készíteni. Ahhoz, hogy a felvitt festék és a felület közötti adhézió megfelelő legyen, a felületet érdesíteni kell. Ez elvégezhető abrazív tulajdonságú szemcsével történő szemcseszórással, vagy csiszolópapírral. Ebben az esetben a járókerék felületének érdesítése szemcseszórással lett elvégezve. A megfelelő érdesség elérése után az alkatrészeket úgy kell elhelyezni, hogy szórás során az alkatrész felületére közel egységes rétegvastagságban lehessen feljuttatni az anyagot. Ezt követően az előkészített felületre felhordható a megfelelő arányban kikevert festék. A felvitt réteg a végleges tulajdonságait magas hőmérséklet hatására éri el. A járókerék festést követően kemencébe lett elhelyezve, ahol a felvitt réteg 80°C - on keményedett ki. A felületkezelést ebben az esetben a járókerék összeszerelése és kiegyensúlyozását követően kell elvégezni a tengely megfelelő kimaszkolása után. Ez azért fontos, mert a kiegyensúlyozás során anyag kerül eltávolításra a járókerékről, és ez megsértené a bevonatot is.
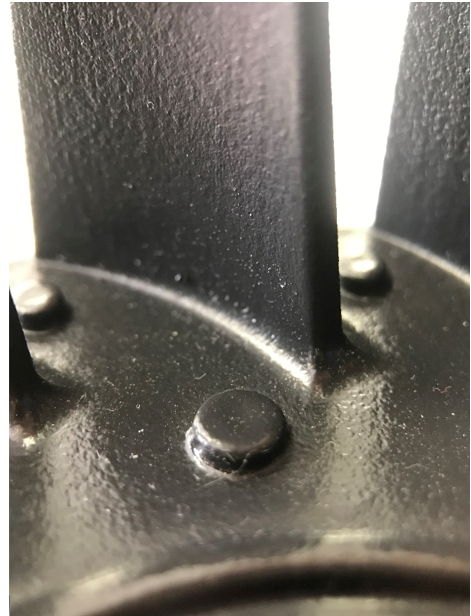
2. Kép: A felületkezelt alkatrész
Összeszerelés
Az összeszerelést megelőzően a járókerék központi furata méretre lett esztergálva, ezzel ellensúlyozva a gyártásból adódó pontatlanságakat. Ez követően a tengely beragasztásra került a furatba. Ehhez a Loctite univerzális felhasználásra szánt HY4090-es kétkomponensű epoxi alapú ragasztója került kiválasztásra. A gyártói honlapon található ajánlás alapján a ragasztó alkalmas eltérő anyagok egymáshoz rögzítésére is, ezek lehetnek fémek, műanyagok, fa, vagy akár különféle kompozit anyagok. A ragasztó megkötés után, jó rezgés és ütésállósággal rendelkezik, valamint magas hőmérsékletet is elvisel a mechanikai tulajdonságok drasztikus romlása nélkül. A gyártó által ajánlott maximális üzemi hőmérséklet értéke 150 °C. Amennyiben megvizsgáljuk a járókerék üzeme közben fellépő hőmérsékletét látható, hogy a ragasztó megfelelőnek tekinthető az adott alkalmazásra. További előnye, hogy jó réskitöltési tulajdonságokkal rendelkezik, ennek értéke eléri az 5 mm-t. [41]
Ragasztás előtt a furat, valamint a tengely palástja csiszolópapírral fel lett érdesítve, ezzel elősegítve a megfelelő szilárdságú kötés kialakulását. A felületek zsírtalanítása a szintén Loctite gyártmányú SF 7063 általános célra szánt alkatrésztisztítóval lett elvégezve. Ezt követően a ragasztóanyag felhordásra került a tengelyre. Az anyag keverési aránya 1:1. A megfelelő minőségű összekeverés a felhelyezhető keverőszár segítségével történt meg. A tengely behelyezése után, kellő mennyiségű száradási idő lett biztosítva a ragasztó kikeményedésére. Ennek értéke gyártói ajánlás alapján szobahőmérsékleten körülbelül 24 óra. A tengellyel együtt ragasztásra került a tengely vállát elfedő takaró elem is. [41,42]
Ragasztást követően a tengely furataiban elhelyezésre kerültek a rögzítésre szolgáló hernyócsavarok. A járókerék az 1. számú mellékletben látható összeállítási rajz alapján lett összeszerelve.
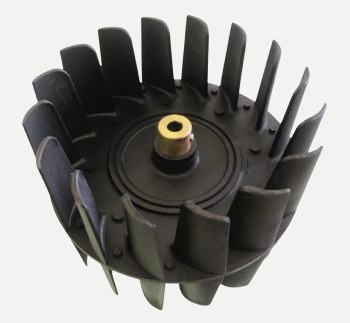
3. Kép: A kész ventilátor kerék
Kiegyensúlyozás
A járókerék üzem közbeni maximális fordulatszáma 2000 ford./perc. Összeszerelést követően nyilvánvalóvá vált, hogy a járókerék ezen a fordulaton történő járatása jelentős rezgéseket idéz elő a motor tengelyén. Ez egyértelműen visszavezethető a gyártás technológiából adódó pontatlanságokra. Ezekből a gyártási pontatlanságokból adódó rezgések megfelelő mértékűre csökkenthetők a járókerék kiegyensúlyozásával.
Ahhoz, hogy a járókerék a kiegyensúlyozó gépre felhelyezhető legyen, szükséges volt egy úgynevezett vendégtengelyt készíteni. Ennek a tengelynek a feladata a járókerék felfekvését biztosítani a gépen
4. Kép: A kiegyensúlyozáshoz gyártott segédtengely
A járókerék felhelyezésre került a tengelyre, melynek rögzítését az előzetesen elhelyezett kettő darab hernyócsavar biztosította. A prizmás alátámasztásba helyezett két végén megtámasztásra került axiális irányú elmozdulás ellen. Továbbá a tengely és a prizma érintkezési felületén kenőanyag lett alkalmazva a súrlódás minimalizálása érdekében. A felhelyezett járókerék egy szíj segítségével lett meghajtva.
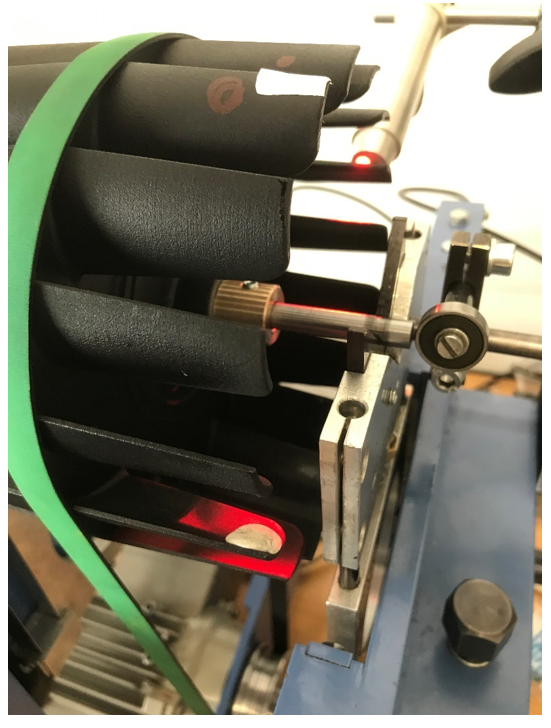
5. Kép: A ventilátorkerék kiegyensúlyozása
A járókerék dinamikusan két síkban lett kiegyensúlyozva. A kiegyensúlyozás próbasúlyos módszerrel történt. A folyamat Gyarmati Károly segítségével lett elvégezve az általa fejlesztett G-Balance elnevezésű célszoftver felhasználásával.
A kiegyensúlyozás során a többlet tömegek a lapátok végéről lettek eltávolítva. Annak érdekében, hogy a lapátok magassága viszonylag egyenletes maradjon az elvett tömeg több lapát között lett eloszlatva.
A fenti eredmények tükrében kijelenthető, hogy a gyártástechnológiából adódó gyártási pontatlanságok megfelelően elvégzett kiegyensúlyozással ellensúlyozhatók. Azonban fontos kiemelni, hogy a tervezés, valamint a gyártás során körültekintően kell eljárni annak érdekében, hogy a kezdeti kiegyensúlyozatlanság mértéke a lehető legkisebb legyen.